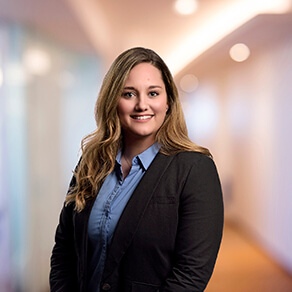
Cost Control Strategies for Your Construction Business
Cost control in construction is the difference between making a profit and absorbing a loss. The rate of inflation is neglected in most construction economics and budgeting which, in turn, leads to project cost overruns in building materials prices, labor wages and machinery rates. With the rising costs of materials and labor, it is increasingly difficult to keep projects within budget. Implementing effective cost control strategies can help construction companies mitigate this risk to help ensure that projected margins will ultimately be realized.
Budget and Planning
Many contractors enter projects with slim margins and take on significant execution risk. All the cost control techniques in the world will fail if you don’t do the proper work when planning the project. Setting realistic detailed budgets is the first step in setting yourself up for success. Look through total expenditures in past projects and come up with estimates on labor, materials, equipment, overhead, permits and any other costs you’re almost certain to encounter. Identify indirect construction-related conditions such as phasing, logistics, schedules and the availability of qualified labor. Foreseeing all costs, not just direct costs, will provide a greater opportunity to negotiate and settle claims for extras from a position of strength.
Effective procurement is another potential area to reduce costs and increase the profitability of a project. Contractors should have a strategic purchasing plan that packages the various components of work to maximize competitive pricing. Unit prices, labor rates and pre-determined alternates should be identified and incorporated into each purchase.
Project Management
Consistent project cost reporting is necessary for effective accounting control. The cost worksheets should be organized in a manner that allows for the comparison between the schedule of values and original cost estimates, and it should account for the latest view of financial status at project completion. Lead project personnel should be responsible for the accuracy of the cost report. The accounting staff should provide valuable assistance and monitor the control process, but overall responsibility for the cost reports should rest with key project management staff. This could simply be a formatted spreadsheet or a report created by the accounting system. Being able to readily identify changes in cost for particular resources is crucial and should prompt questions about bad rates, operational inefficiency and unidentified scope changes.
There should be weekly or, at a minimum, monthly project status reports and meetings, which provides senior management with a high-level view of the project, including profit estimates. Other relevant information to be communicated monthly is an updated project schedule, a list of unprocured trades, outstanding billings and critical client and subcontractor issues. The better you communicate with your team, and vice versa, the more likely you are to stay on budget. If your team understands what they need to do and when, and you provide them with the resources they need when they need them, you can avoid busting the budget. Through constant monitoring, you will reduce the chances of surprises when it comes time to review the completed job.
Post-Job Completion
Whether you stayed on budget or not, you should conduct a post-project review of how well you controlled costs once you wrap up a project. Get together with key parties and go over the initial budget compared to final expenditures. Discuss what went right and what didn’t and what adjustments should be made on the next project.
Cost control starts during the bidding or proposal process and continues until the project closeout. Managing costs throughout the life of a project requires effective foresight, expertise, organizational communication, accurate and organized reporting and a reliable accounting system. Most importantly, it requires effective teamwork among all personnel. Well-run companies have strong procedures for detailed recording and forecasting of costs, as well as the evaluation, approval and processing of company commitments and invoices. By taking a proactive approach to cost control, construction companies can improve their bottom line and position themselves for long-term success.
Contributing author: Kaitlyn H. Axenfeld, CPA/CFF, CFE, has extensive experience providing audit, review, compilation and advisory services to a wide variety of clients with a focus on the construction and manufacturing industries. Kaitlyn specializes in forensic accounting and consulting services, including litigation support to law firms and privately held companies in fraud detection, damage calculations and prevention matters. If you have any questions or need any assistance, please contact Kaitlyn at kaxenfeld@dmcpas.com.