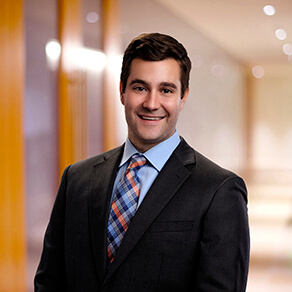
Fraud in the Manufacturing Workplace
The manufacturing industry is often more vulnerable to the exposure of fraud and corruption than other industries. The Association of Certified Fraud Examiners (ACFE) determined in its 2022 Report to the Nations on Occupational Fraud and Abuse that the annual cost of fraud globally is approximately $4.7 trillion, with an average loss per case of $1.78 million. The median loss caused by fraud for manufacturers totaled approximately $177,000 and was $150,000 for manufacturers with fewer than 100 employees. Fraud schemes involving theft of inventory and equipment, warranty claims and product quality pose a particular susceptibility to the manufacturing industry. Executives and managers at manufacturing companies must be aware of these prevalent types of fraud in the industry, as well as the controls that are necessary to detect and prevent such activity.
Inventory Fraud
Inventory, or “noncash” frauds, are among the most common fraud schemes reported by manufacturers. Incidents of noncash theft often involve the theft of inventory or equipment. Inventory theft generally occurs in the following ways:
-
- Theft of inventory between locations (asset requisition and transfers);
- Falsification of shipment records (purchasing and receiving schemes); and
- Sending inventory to a fictitious location and subsequently reselling the inventory (false shipment of inventory).
Some important indicators of inventory theft can include unusual inventory shrinkage, physical inventory counts not consistently agreeing to system-produced reports and fluctuations in inventory that are not reflected in sales and purchase activity. It is important to monitor inventory through regular counting cycles, organized warehouses and strong record-keeping. Investigating variances and maintaining proper internal controls surrounding picking, packing, receiving and stocking procedures are also critical when mitigating the risk of fraud. Checking metrics and ratios against past performance and manufacturing industry benchmarks that allow for the detection of inventory fraud can also be a helpful preventative measure. These metrics and ratios include gross margin as a percentage of sales, days in inventory, inventory as a percentage of total assets and inventory returns as a percentage of annual sales. Additionally, utilizing technology such as cameras, alarm systems and electronic locks that are accessed with identifying key cards is also highly recommended.
Product Quality Fraud
Product quality fraud is a common avenue for fraud in the manufacturing industry and involves the use of inadequate materials in the production of finished goods. It is not uncommon for manufacturers to subcontract both essential and non-essential production procedures to third parties throughout the supply chain process. The altering of tests by these third parties to meet regulatory standards, such as product safety and environmental protection laws, or to meet quality control standards of the manufacturer company selling the product, are common examples of when this type of fraud might occur.
Proper due diligence must be employed when securing subcontractors. Mitigating the vulnerabilities related to a company’s product, such as the substitution of inferior materials and product counterfeiting, are critical to maintaining the desired product quality and the integrity of the company. Subcontractors should never be used without performing proper due diligence. Background checks of subcontractors can be a great avenue to investigate reputations and incidents of misconduct. Implementing proactive quality control measures and conducting fraud risk assessments throughout the supply-chain levels are also important to identify areas of potential weaknesses, including fraud, and can significantly reduce potential losses caused by misconduct.
Warranty Claims Fraud
Under a warranty, manufacturers typically agree to repair or replace defective products at the expense of the manufacturing company. Customers and service centers have a wide variety of fraudulent schemes for exploiting warranty programs, including, but not limited to, duplicate claims, false claims and false defects. Service centers are generally reimbursed by manufacturing companies for labor costs related to warranty repairs. Some complex schemes may include service centers falsifying warranty claims to receive these labor cost reimbursements for unrelated work where additional revenue would not normally be received. Counterfeit products can also find their way into warranty claims in these types of fraud schemes and can even include genuine serial numbers.
Key methods in detecting false warranty claims include using data analytics to identify suspicious patterns and inspecting returned products in detail to confirm the legitimacy of the claim. Recognizing fraudulent claims can save manufacturing companies significant losses.
Conclusion
It is important that owners, executives and managers working in the manufacturing industry continuously enhance fraud risk management and internal controls to prevent and detect fraud. If you are interested in learning more about internal controls related to the manufacturing industry, please contact our experts at https://www.dmcpas.com/leadership/ and we can help you navigate any concerns and questions surrounding these procedures.
Contributing author: Robert C. Reeves, CPA, CFE, is an audit manager with over seven years of experience providing audit, review, compilation and consulting services to a variety of clients with a focus on the manufacturing, construction and architectural and engineering industries. Bob also specializes in providing audits of employee benefit plans, working with clients to help identify and resolve accounting issues, and has an extensive background discovering, investigating, and resolving fraud cases.