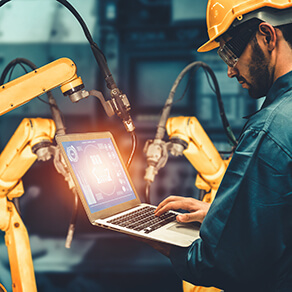
How Automation Can Help Your Labor Shortage
The COVID-19 pandemic was another hit to manufacturing’s labor shortage. For manufacturers affected by the shortage, investing in automated equipment may seem like a smart alternative to relying on people. Automation can reduce a company’s human resource headaches and decrease compensation costs.
Finding Labor
In today’s tight labor market, good help can be hard to find. According to a study by Deloitte and The Manufacturing Institute (a partner of the National Association of Manufacturers), the manufacturing skills gap in the United States could result in 2.1 million unfilled jobs by 2030. The study also found that digital transformation in the manufacturing industry will redefine work for humans.
Automated equipment can help manufacturers meet production demands, especially in remote areas with limited sources of trained workers. Automating your plant may be easier and less expensive than, say, training existing workers or luring skilled people from urban areas to work for you.
Using Robots
Robots, if properly programmed and integrated into the surrounding systems, can perform certain tasks faster and with fewer errors and less waste than humans. Automated equipment is well suited for large production runs, as well as repetitive, dangerous and labor-intensive tasks. Examples include welding parts, performing pick-and-place tasks and cleaning up chemical spills. But if you run small batches of custom work, it might make sense to stick with humans.
In addition, automated production lines and the use of robots can help differentiate your business from competitors. For example, press releases and social media posts about your investment in automated equipment could boost your brand’s image as an innovator and/or a high-quality producer.
Employees are seldom satisfied doing the same mundane tasks, day after day. By automating repetitive tasks, your workers are free to perform high-tech custom work and program robots for the next run. In addition, assigning dangerous or strenuous work to robots can reduce work-related stress, accidents and health issues among employees. Of course, morale benefits will be tempered if automation results in the elimination of several positions or employees fear their jobs are in jeopardy.
Automation isn’t just for your manufacturing floor. Robotic process automation (RPA) can help the administrative side of your business. RPA refers to software tools that automate repetitive, rule-based human tasks. For example, properly designed RPA solutions can compile necessary billing data (from multiple systems, if necessary) and create accurate invoices in a matter of minutes. It can also be used to generate and analyze work-in-progress reports to ensure that jobs are progressing profitably, and to provide an early warning of cost overruns and other potential problems. Finally, RPA can be used to automate a variety of tasks involved in recruiting, onboarding, payroll, and other labor- and document-intensive HR processes.
Understanding Downsides
The biggest downside to automation is the initial cost. So, it’s critical to crunch the numbers before making the investment. Rather than purchase equipment outright, consider financing or leasing the equipment to spread the cash outflows over five to ten years. However, financing costs could increase significantly if interest rates increase or lawmakers make changes to the federal tax deduction for interest expense.
Also consider how much it will cost to train employees to operate, program and repair the equipment, along with incremental insurance, utilities and repair costs. You may even need to revise your production line to avoid unexpected bottlenecks that may occur as automation alters throughput, cycle times and setup times.
Though machines don’t complain or call in sick, they do break down and show wear, necessitating a formal maintenance program. If you aren’t disciplined enough to follow a maintenance schedule, consider leasing the equipment from a company that will also maintain it.
Additionally, as with any type of technology, it’s important to evaluate cyberthreats that automation might bring. Could your robots be hacked or infected with a virus that shuts down your production line?
Embracing the Future
Technology is the future of many manufacturing businesses. The robotic capabilities in current use are considered to be a boon to progress and will make your company innovative. Start with a few robots and take it from there. Contact us to review the costs of buying, implementing and maintaining automated equipment and RPA software.