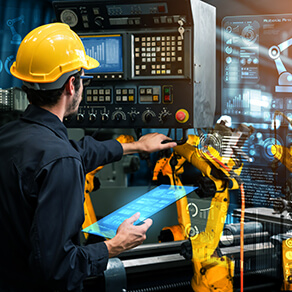
How To Manage WIP Inventory
Work-in-process (WIP) inventory is an important entry on a manufacturer’s balance sheet. Monitoring WIP is critical not only to ensure that your financial statements are accurate but also because it serves as a useful metric for tracking your company’s performance.
What’s WIP?
Simply put, the term “WIP” refers to all inventory in the stage between raw materials and finished-product inventory. Any time direct labor is applied to raw materials that aren’t yet ready to be sold to customers, their production costs (raw materials, direct labor and factory overhead) are reported in WIP. The formula for estimating ending WIP in an accounting period is relatively simple: Beginning WIP + production costs – cost of goods manufactured (COGM) = ending WIP Suppose, for example, that a manufacturer’s WIP at the beginning of a quarter is $100,000. During the quarter, its production costs total $250,000. The manufacturer’s COGM (the production costs for goods that are available for sale) is $200,000. It’s ending WIP, therefore, is $150,000 ($100,000 plus $250,000 minus $200,000).
What Are the Benefits of Tracking WIP?
Estimating and monitoring WIP provides several important benefits, including:
Reporting More Accurate Inventory Values. Getting a handle on WIP helps ensure that your inventory is valued accurately on your balance sheet. If you undervalue WIP, you’ll overstate your COGM, which can distort your financial performance.
Reducing Reliance on Physical Counts. Assuming you have systems in place for tracking and estimating production costs, valuing WIP using the formula discussed above allows you to rely less on costly physical counts of WIP inventory at various stages of the manufacturing process. Physical counts provide important benefits — such as identifying damaged or stolen goods and revealing reporting errors — but properly tracking WIP allows you to reduce your reliance on them.
Identifying Trends and Red Flags. WIP is a valuable metric that can reveal significant trends, helping you spot red flags and address them before they damage your profits. For example, excessive WIP can forewarn of bottlenecks in your supply chain or manufacturing process. A large amount of WIP also means higher storage costs and a greater amount of capital tied up in nonsalable assets. And more WIP means more unfinished products, which present a greater risk of damage, loss, expiration or obsolescence while awaiting completion.
Is There an Optimal Level of WIP?
Generally speaking, in terms of cost and efficiency, the lower your WIP, the better. In some cases, however, a certain level of WIP can be a good thing. For example, having some WIP for employees to work on can minimize downtime when there are delays in the supply chain. And too little WIP can mean excessive completion times for finished products.
The optimal level of WIP varies from manufacturer to manufacturer. What’s right for your business depends on several factors, including the number and types of products you manufacture, the nature of your supply chain and operations, and your inventory management strategies.
Getting Help
To manage WIP effectively, you need to be able to measure it. That means you’ll need to have the ability to track the costs of raw materials, direct labor and factory overhead at various stages of the manufacturing process. Contact us and we can help ensure that you have systems in place for collecting the data needed to optimize your WIP.