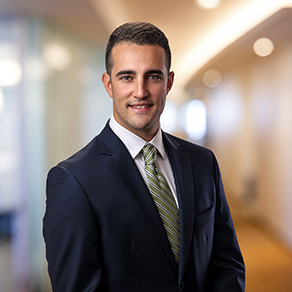
Managing Indirect Costs in the Construction Industry
The construction industry operates under complex cost structures, making it essential to accurately allocate indirect costs to ensure profitability and accurate project management. Unlike direct costs, such as materials and labor, indirect costs encompass overhead expenses that support multiple projects but are not directly attributable to a single construction site.
What Are Indirect Costs?
Common indirect costs in construction include:
- Equipment depreciation
- Repairs and maintenance of equipment
- Equipment and tool rentals used on multiple jobs
- Insurance costs
- Temporary facilities (trailers, storage, security)
- Salaries for supervisors and administrative staff who manage and support multiple projects
- Legal fees and permits
Since construction projects often vary in size, duration and complexity, companies must use strategic allocation methods to distribute overhead costs fairly across different projects.
A thoughtful and consistent approach to allocating indirect costs ensures:
- Competitive Bidding: Helps set realistic contract prices
- Financial Transparency: Ensures proper reporting and profit estimation
- Effective Resource Management: Guides cost-saving decisions
- Compliance and Tax Considerations: Correct allocation supports financial audits
Improper allocation or lack of budgeting for indirect costs can lead to underpricing bids, resulting in financial strain, overpricing and loss of competitive advantage.
Common Indirect Cost Allocation Methods for Construction
1. Percentage-of-Project-Cost Allocation
This method assigns indirect costs as a flat percentage of total project expenses. For instance, if overhead typically runs at 10% of project costs, that percentage is applied proportionally across all ongoing projects.
Best for: Small, simple and fixed fee projects.
Pros: Quick and simple to calculate.
Cons: Less accurate for projects with non-proportional costs and ignores the actual resource consumption.
2. Direct Labor Hours or Costs Allocation
Since labor is a major cost driver in construction, companies often allocate indirect costs based on total labor hours or labor costs per project. Projects requiring extensive labor naturally absorb a larger portion of overhead.
Best for: Labor-heavy projects with less equipment utilization and variable labor costs.
Pros: Easy to track and calculate when labor hours are recorded.
Cons: Doesn’t account for equipment or site-specific costs, large variations in labor hours can skew allocations and ignore non-labor drivers.
3. Equipment Usage Allocation
Heavy machinery and leased equipment contribute significantly to indirect costs. Construction firms allocate expenses based on actual hours used, spreading costs across multiple projects that utilize the same equipment.
Best for: Machinery-intensive projects.
Pros: Allocates equipment-related indirect costs such as depreciation and precise recovery of equipment costs.
Cons: Needs accurate tracking of machine hours, neglects non-equipment-related overhead.
4. Activity-Based Costing (ABC) for Specialized Projects
ABC assigns overhead costs based on activities that drive indirect expenses. For example, if safety inspections are frequent on high-rise projects, those projects bear higher compliance costs than smaller residential builds.
- Best for: Complex, large-scale projects.
- Pros: Highest accuracy. Allocates based on multiple activities and can provide good insight into resource consumption and efficiency.
- Cons: Resource-intensive, complex to implement.
5. Square Footage or Site-Specific Allocation
For large-scale developments, indirect costs may be allocated based on the total project footprint, ensuring that larger projects absorb a proportionate share of general overhead.
- Best for: Multi-site jobs.
- Pros: Directly ties overhead, such as trailers and utilities, to site usage.
- Cons: Only applies to space-based costs.
Common Challenges in Construction Overhead Allocation
Construction companies often face hurdles in tracking and allocating overhead due to:
- Fluctuating project timelines and scope changes;
- High variability in indirect costs (e.g., seasonal labor costs, fuel prices); and
- Interdependencies between multiple projects using shared resources.
To address these challenges, companies should regularly review their allocation methods and update cost drivers based on real-time data. Companies should incorporate fluctuating indirect costs into their budgeting based on historical analysis and anticipated market changes, ensuring that all costs are accurately reflected in their bids.
Conclusion
Allocating indirect costs is more than just an accounting exercise—it’s a strategic necessity in the construction sector. By implementing accurate allocation practices, construction companies can improve financial performance, optimize project bidding and pricing and maintain profitability amid fluctuating market conditions. Contact us with any questions regarding the implementation of these practices.
Contributing author: Timothy L. Corapi, CPA, is an audit senior manager with extensive experience leading engagement teams in the execution of audits, reviews, compilations, and other attest services. He has a strong background serving clients across the construction, automotive dealerships, life sciences and manufacturing industries. For more information on this topic, you may contact Tim at tcorapi@dmcpas.com or (315) 472-9127.