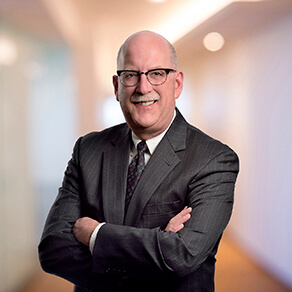
How Do I Get Out of Doing a Physical Inventory Count?
How do I get out of doing a physical inventory count? This is a question we hear from our clients at least once each year. With the impact of the pandemic on staffing and other pressures on productivity, exploring a company’s alternatives to physically counting its entire inventory via an annual wall-to-wall exercise has attracted even more attention.
For companies where inventory represents a material asset on the balance sheet, and in instances where an audit is performed by your CPA, a physical count is a required step. One level down at the review level, the CPA will inquire of management whether inventories have been physically counted and, if not, how inventory quantities were determined. They will also likely ask whether adequate procedures were used to take the latest physical inventory and on what date that inventory was taken.
The objective of a physical count is to adjust the company’s perpetual inventory records to ensure this detail faithfully reflects quantities on hand at the balance sheet date. It is possible to reduce or eliminate the annual physical counting process through a process known as cycle counting.
Is Cycle Counting for Your Company?
Effective cycle counts require the same procedures used in an annual physical inventory, including instructions, assigning responsibilities, training and counting, but rather than counting all of the inventory once at one time, the controller can schedule counts based on location, inventory balances, available personnel resources or other criteria that fit the company’s needs over the course of the year.
The “ABC” concept is considered, which emphasizes counting “A” and “B” items, which are higher-dollar value or more significant items that may be counted once a month or several times each year. “C” items might represent small parts that may be counted once each year due to the minimal impact count variances might have on the overall balance sheet.
The most important part of the process involves the controller developing a system to ensure that all inventory is counted at least once during the year, with the cutoff date demanding increased scrutiny to coordinate the counting of all items at the appropriate time. By the time one year has passed, 100% of inventory items have been counted at least once, and the perpetual adjusted for any count variances found.
Benefits of Implementing a Cycle Count Program:
-
- Eliminates the requirement for a complete shutdown of shipping, receiving and production.
- Identifies shortages or errors more quickly after occurrence so that determining the causes is facilitated.
- Reveals damaged or substandard materials more quickly, which may preclude a production shortage.
- Provides an incentive for more accurate recording of issues and receipts because personnel know that counts are conducted more frequently.
- Avoids serious year-end adjustments occurring, making interim financial statements more accurate.
Dannible & McKee, LLP has extensive experience assisting our clients in evaluating a company’s internal control environment for implementation of cycle counting procedures and in designing a process and program. If you feel the time has come to explore such an upgrade, now is the best time to contact us to discuss the matter, as we are right at the beginning of the year with adequate time to plan, evaluate and execute your new cycle counting program in time to reduce your physical inventory count at the 2022 year-end.
Contributing author: Brian W. Johnson, CPA, CFE, is an audit partner at Dannible & McKee, LLP. Brian has over 36 combined years of experience providing audit and accounting services to both private and publicly-held domestic and foreign companies. He has extensive experience providing fraud and forensic examinations, as well as SOC audits, internal audit outsourcing and internal controls evaluation and consulting. For more information on this topic, contact Brian at bjohnson@dmcpas.com or (315) 472-9127.